Be the first! Get the latest news and updates - Subscribe to our newsletter!
Browse our product catalog
Popular product categories
A good starting point could be…
Installers

All relevant information for Installers about energy saving CoreLine LED luminaires, retrofit LED lamps and LEDtubes and conventional lighting.
Lighting specifiers

The Signify Specifier hub: home to innovative lighting projects, training, tools, and events for architects, lighting designers, and engineers.
CSI

Become a Philips partner today and gain access to a wide range of products, systems and innovative solutions that your customers will love.
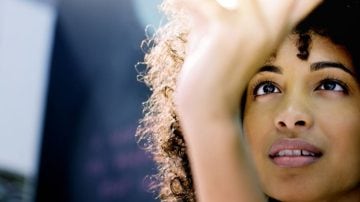
Lighting Academy
Lighting Academy offers a comprehensive range of educational resources to advance your lighting knowledge.
The educational lighting materials are provided by world-class lighting experts and professionals. Self-learning has never been easier than it is now. Be brighter by the day!